CADCode Systems’ OptiNest™ optimization offers advanced part cutting control for nested based manufacturing. With OptiNest you’ll get more parts out of your sheet goods and spend less time making them. We optimize to maximize material yield and to minimize machine cycles.
Save materials, save time, save money.
Optimizing is more than just getting the largest number of parts out of the smallest amount of material. It’s also about the amount of time spent cutting out those parts. OptiNest maximizes the use of materials and minimizes machine time while also taking into account graining, small part locations, and the other factors that are vital for successful part machining.
Machining small parts is a big deal.
Because parts are “fixed” in place on the router’s table by vacuum, and vacuum is a factor of surface area, the smaller the part, the less pressure there is holding that part in place. The high rotation speeds of a cutting bit can easily knock a small piece loose if it isn’t held securely in place. OptiNest provides a number of options for controlling these small parts, from tabs, onionskinning, and multiple machine passes to smarter nesting algorithms that connect small parts to larger parts until their final release.
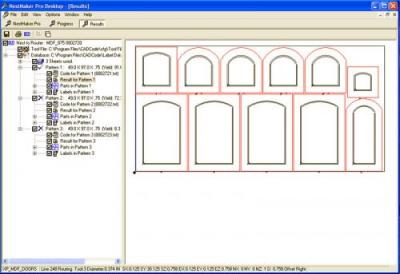
Stay in control of the optimizer’s results.
For special situations where you need to adjust the optimization results, the OptiNest Panel Editor allows you to view the cutting patterns and move the parts around, and will automatically generate a new cutlist and fresh machining programs for the modified patterns.
Easy nesting of non-rectangular shapes.
Nesting makes it simple to cut out non-rectangular shapes. You can include any shape in a job and OptiNest will consider the smallest rectangle available to contain that shape and place it into the nest. If you create lots of irregularly shaped parts, our optional non-rectangular or “true-shape” nesting will fit shapes within shapes with minimal space between parts to get more parts from each sheet.
Multiple operations with one click.
In nesting, cutting out the parts is just one more machining task that happens in conjunction with drilling, routing, dados, pocketing, and so on. Cutting out the parts is fully integrated with other operations to optimize the movement of the router head(s) to minimize travel and time spent to cut out the parts.
Do more at the click of a button than just optimize.
When you process a job, depending on the processes chosen, CADCode will also create all of the machining programs for the nest and each part within the nest, generate part labels, and generate reports, all at the same time, all with one-button simplicity.
CADCode’s OptiNest is an integrated in CADCode’s nested-based manufacturing solutions.
NestMaster™
NestMaker™
NestLink™